SST Shop Talk
In Depth Discussion In Planning CNC Programs

Understanding the Computer Numerical Control Machine as well as learning the method of programming these machines is not enough to maximize the capability of these devices. Even if you are proficient on those two stated above, proper understanding of the step by step procedures is still important.
In this article we would talk about the step by step procedures of programming Computer Numerical Control Machines which is recommended by the most experienced CNC Machine Operators and programmers.
Step by Step procedures in planning of a CNC program
Whenever we try to program a Computer Numerical Control Machine the first thing that the Machine operator should consider is the blueprint of the part we are trying to manufacture. Proper understanding and reading of a blueprint is a basic and the most important skill in the manufacturing Industry that engineers, managers, CNC machine operators as well as CNC programmers should know about.
Proper understanding of these blueprints should help the CNC machine operator as well as the programmer to use the appropriate CNC machine to be used.
The second step on the proper programming of a Computer Numerical Control Machine is by selecting the appropriate type of Machine that will be used. This is where the proper understanding of each machine type comes into play. Knowing the type of design, specifications as well as features of a machine will help you on choosing the appropriate one.
The third step would be the analysis of the operations or the setup sheet. The setup sheet is used to describe the necessary processes needed to create the parts on a CNC machine. The setup sheet includes the proper machine sequence and also the tools and cutting data to be used. Specifications written on the setup sheet aids the programmer on the proper algorithm needed by the Computer Numerical Control Machine.
The fourth step on the step by step requirements would be the proper selection of the tools required to create the parts. This step is important on the industry manufacturing practices, basically the tools to be chosen is based on the common sense and Good CNC operators and programmers should be aware of them. Usually there is a certain checklist on this step, the most important point of this checklist would be knowing the material to be machined as well as its characteristics.
Fifth step would be the calculation of the cutting data. Proper calculation is one of the important steps in the planning process. This is where the spindle speed, federate value, cutting speed and the depth of cut is calculated to fit to the specifications in the blueprint.
Sixth step would be the actual programming process, this is also the step where the proper Units are inserted into the programming algorithm of the Computer Numerical Control Machine. This is where we incorporate all the codes that are needed to run the whole CNC machines in the CAD software.
Programming Considerations
In order for other programmers to analyze and append your algorithm, it is important to have certain programming considerations. These program considerations were suggested by experienced Computer Numerical Control Machine Programmers and Operators.
First it is important that you develop a programming technique that will be readily understood by other developers, with a good programming technique programs could easily be appended if there are any errors.
Second, it is also important to proofread all programs for typographical errors before being executed in the CAM software, this is to ensure that the CNC machine would operate its desired operation. And most important of all is to keep your programs as simple as possible in order for the machine to process the instructions faster.
The Programmer
The first person is the CNC programmer. He is like the "playmaker". He will create the programs that the CNC machines are intended to execute. Since the programs are in the form of CNC codes fabricated like sentences, he should have mastered these codes because they work like a different language. The regular CNC machine can use up to 50 codes, so that's like learning 50 new words for the newbie.
Also, the programmer should have at least and engineering or machining degree. Remember that the CNC machine will only execute WHAT IT IS PROGRAMMED TO DO. If the program is wrong, the whole operation goes down the drain with it. Moreover he should also be flexible and have a fast turn-around because a CNC machine is often used to machine a huge selection of different work-pieces.

The Technician
The third person that will need is the CNC technician. Although this may still be the programmer, it is more convenient to always have a technical expert on-call because in the long run, you may have more than one CNC machine and you may need to prioritize over the other in case both gets crippled at the same time. Just like the programmer, the technician should also be flexible and articulate. CNC offers a lot of complexity when it is running right, how much more if it is behaving badly?
So, if you are having job openings for positions that need to be handling a CNC machine, ask the applicants first to do a demo for you and make sure that during the demo, they know what they're doing. An exam may also do wonders too. If they have no experience with any kind of CNC machine, it is advisable that you encourage them to take short courses on CNC.
Eighty-hour courses are available online and hey, it is better than nothing. Experts even encourage employers to hire CNC machinists who have finished AND PASSED the National Occupational Competency Testing Institute (NOCTI) assessment just so they could be sure that their CNC machines will go to good hands. After all, a CNC machine is still an asset.

The Operator
The second person that you need is the CNC operator. He will simply recheck the programs loaded to the machine and push the right buttons to get the work done. However, thinking that a CNC operator can have little or NO SKILL AT ALL is wrong. A CNC machine operator must have at least basic machining skills and he should have undergone some form of training to run a CNC machine.
These machines can produce very intricate motions, making it possible to make shapes that cannot be created on conventional machine tools. So, the operator should foresee this complexity and know how to cruise with it. The skills that an operator must have though, are lesser compared to the operators of conventional machine tools.
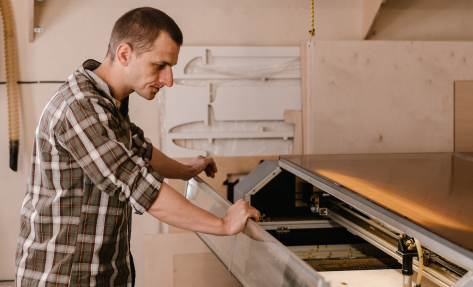
